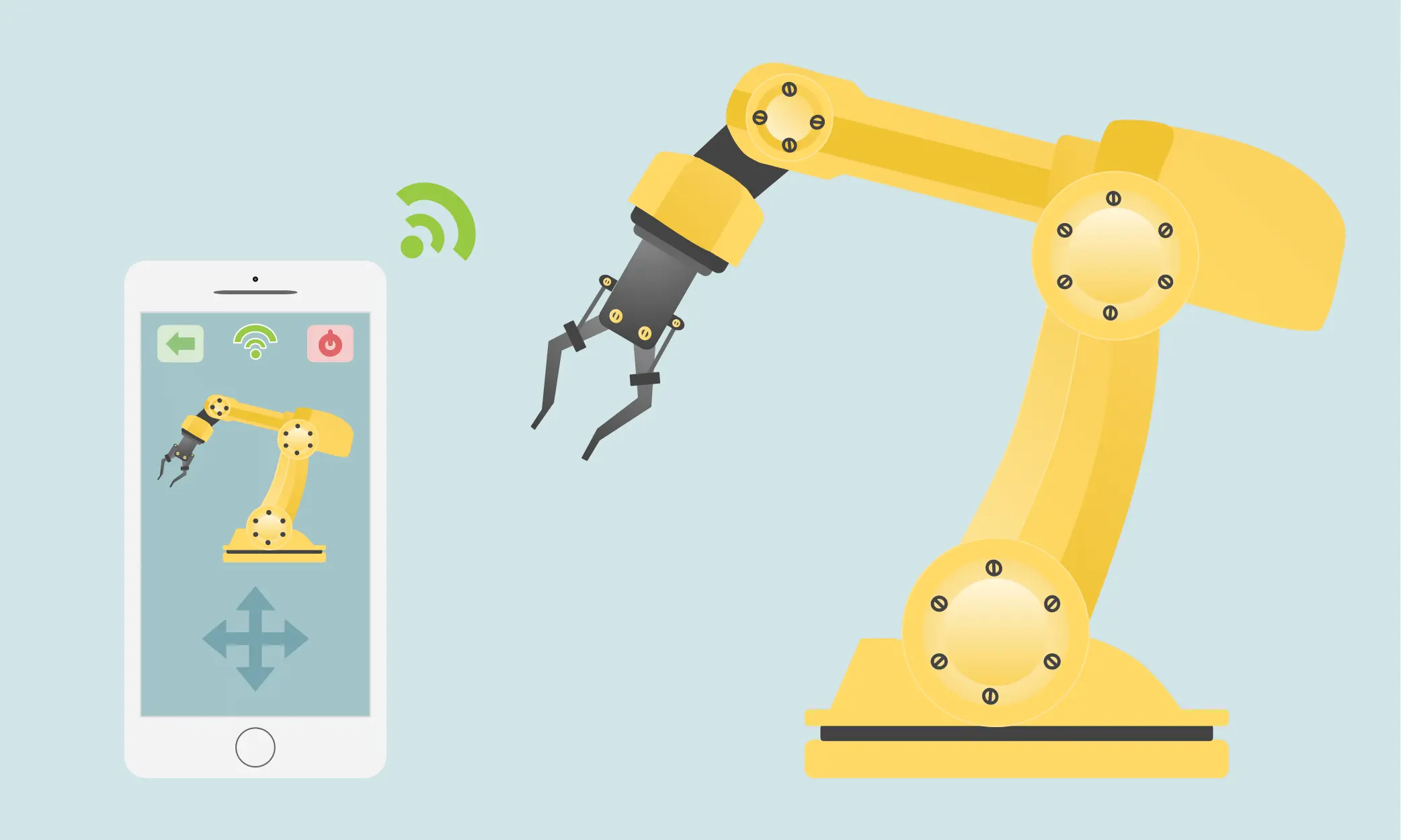
Load cells and force sensors have been around for many years. However, these mature technologies are continually adapting to the needs of emerging technologies like robotics. Admittedly, robotics isn’t the latest technology either. Robots can be traced back to the early ’60s when automotive production lines began using them. Over decades, robots have reached into many other industries, including medical technology. It is these new applications that keep robotics in the category of emerging technology.
“Load Cells” vs. “Force Sensors” in Robots
Before discussing the applications of force sensors and load cells in robotics, it helps to clarify these terms. The term “load cell” primarily describes a device that measures weight. The term “force sensor” mainly refers to a device that measures pressure. Since pressure is nothing more than weight per unit area, the two terms describe the same physics.
Typically the robotics field prefers the term force sensor while the weight measurement field uses the term load cell. Perhaps this is because weight measurement usually measures forces due to gravity (or loads); by contrast, control systems in robotics receive force data from any direction (such as a robotic grip on an object). Also, load cells generally (but not exclusively) imply strain electronics bonded to steel structural elements. Force sensors for robotics, on the other hand, can be very tiny, in fact sometimes microscopic; Also they employ physical properties other than strain.
Robotics Industry Trends for Force and Tactile Sensors
In addition to clarifying terms, it is likewise important to understand current trends in robotics. Right now in the industry, Collaborative Robots (Co-Bots) are seen as the future of manufacturing. The reasons are self-evident.
- These robots save both time and money, being available for product throughput 24/7.
- Robots are scalable and adaptable resources. They can be used for high production, high volume jobs one day, then scaled down for a specialized low volume job the next day.
- The field of robotics creates jobs. Although robots replace production line workers, human resources must keep them ready to do different jobs in different parts of a factory. The map in Figure 1 shows the deficit of robotics talent in 2018. These deficits are projected to grow [1].
Business predictions assert that the future new robot installation rate will climb by 6%/yr over the next few years. The chart in Figure 2 demonstrates this [2]. The global robotics and autonomous systems market is expected to grow to $275B by 2025 [3]. The recent pandemic has only furthered this need for non-human service workers.[14] The need for load cells and force-sensing technology will grow right along with it.
New Applications for Robotic Force and Tactile Sensors
Until recently, the primary application for robots has been safety when working close to humans. However, new applications of force and tactile sensors are evolving far beyond being a safety net. New levels of precision are the latest innovations in industrial robotics. With modern tech sensors and advances in control software, robots are developing a “feel” for what they touch. Moreover, most robots today, especially collaborative robots, have force and torque sensing abilities.
These new levels of precision and accuracy allow collaborative robots to take over many delicate production tasks such as:
- Gripping
- Grinding
- Deburring
- Polishing
- Product assembly
- Packaging products
- Quality/Product testing
A force-sensing technology on the rise for rapid order fulfillment is “gripping”. Gripping technology is expected to be the fastest-growing warehouse automation technology in the US by 2020 [4]. The combination of machine learning software, improvements in force-sensing technology, and easier to program, application-centric solutions are critical to this growth.
Another example from the list above made possible by tactile sensing technology is product assembly. Modern sensors enable processes with very close tolerances or clearance around parts. An example is the automotive manufacturing process of inserting pistons into an engine. Currently, robotic vision systems are not capable of providing the precision needed for these jobs. Instead, force-sensing devices find the precise tool center point for use in inserting the piston [5] with extreme accuracy. Yes, these “touch and feel” capabilities are exciting advancements for the venerable force sensor, as they allow robots to assume some very human aspects of getting jobs done.
Innovations in Robotic Load Cell and Force-Sensing Technology
Advances in force sensor technology are not the only innovations that are moving the field of robotics forward. As previously mentioned, innovations in both programming and materials are also creating new opportunities for robots. This section explains further.
Programming Innovations
Machine learning software advancements are lending new flexibility to robotics along with new force sensing tech. Robots have matured to the point where they can adjust to real-time variables without specialized programming. The machine learning algorithms in robotics software are self-teaching. A human trains the machine to perform the process merely by dragging the robot arm along with him. The robot will then mimic the motion and learn more from each iteration until it’s doing the job to specification. The accuracy and precision of its internal force-sensing devices combined with the machine learning algorithms do all the heavy lifting.
Materials Innovations
Lastly, when discussing innovations in force sensor tech for robots, it is important to mention new applications for materials. Graphene is a material that was first isolated in 2004. Innovators are now widely realizing its value, including for pressure sensors.
What is graphene? Graphene is a one-atom-thick layer of carbon atoms in a hexagonal lattice arrangement; it is the building block of graphite (the same stuff in your #2 pencil). Although it is the thinnest material known to man at just one atom thickness, it is very strong (about 200 times stronger than steel). It is also highly conductive of both heat and electricity [6]. Because of its physical properties, graphene opens the door for the development of nanoscale sensors. These make possible cell-sized robots for medical research, diagnosis, and many more new discoveries over time.
In general, graphene sensors are capacitive or piezoelectric sensors. (See An Overview of Load Cells and Comparing Strain Gauges to Piezoelectric Sensors.) That is, they create an electric field under applied pressure. They function with very low power and are far less influenced by temperature than common strain gauge sensors. This public document [7] explains the challenges of fabricating graphene sensors and some advances in the adaptation of the material.
As an example of the versatility of graphene in sensor technology, researchers in 2016 demonstrated a biocompatible pressure sensor made from mixing graphene flakes with cross-linked polysilicone (silly putty) [8].
In the future, its micro size, superior strength and favorable response in unfavorable ambient conditions will bring graphene to the forefront of sensor applications in robotics.
Conclusion
As this article demonstrates, load cells are advancing the field of robotics immeasurably. New programming techniques combined with new materials are enabling high-precision and nanoscale applications. What was once science fiction is now becoming reality.
Sources
[1]
“The Global Talent Crunch, Future of Work,” Korn Ferry, 2018
[2]
Executive Summary World Robotics 2019 Industrial Robots, International Federation of Robotics (IFR)
[3]
“Global robotics market will triple to $275bn by 2025 driven by cheaper, smarter machines, says GlobalData,” Global Data, Press Release April 11, 2019
[4]
“Gripping M&A – The extending arm of Robotics,” DC Advisory, January, 2020
[5]
Isaac Maw, “Eye Spy: The Basics of Robotic Vision Systems” engineering.com, July 16, 2018
[6]
“What is Graphene?“, Graphene-info.com, March 2019
[7]
Christian Berger, Rory Phillips, Alba Centeno, Amaia Zurutuza, Aravind Vijayaraghavan “Capacitive pressure sensing with suspended graphene–polymer heterostructure membranes,” Nanoscale Journal, Issue 44, 2017
[8]
Coxworth, Ben (December 9, 2016). “Silly Putty Smartens Up, With a Dash of Graphene”. newatlas.com. Retrieved April 30, 2017.
[9]
Keith Shaw, “The Robotics Sector in 2020 and Beyond: Predictions from Industry Gurus,” Robotics Business Review, December 16, 2019
[10]
Tanya M. Anandan, “Force and Tactile Sensors Give Robots a Feel for the Job” Robotics Online, July 2018
[11]
Xu, Yang; Guo, Zhendong; Chen, Huabin; Yuan, You; Lou, Jiechao; Lin, Xiao; Gao, Haiyuan; Chen, Hongsheng; Yu, Bin (2011). “In-plane and tunneling pressure sensors based on graphene/hexagonal boron nitride heterostructures“. Applied Physics Letters. 99 (13): 133109.
[12]
Brian Dunn, “Load Cells: Introduction and Applications,” 2016
[13]
Dragos George, “Force Sensors Used in Robotics,” SmashingRobotics.com, October 2012
[14]
Théo Schöpfer, Dr Reza Etemad-Sajadi, “The clever use of robots during COVID-19,” EHL Hospitality Insights, 2021