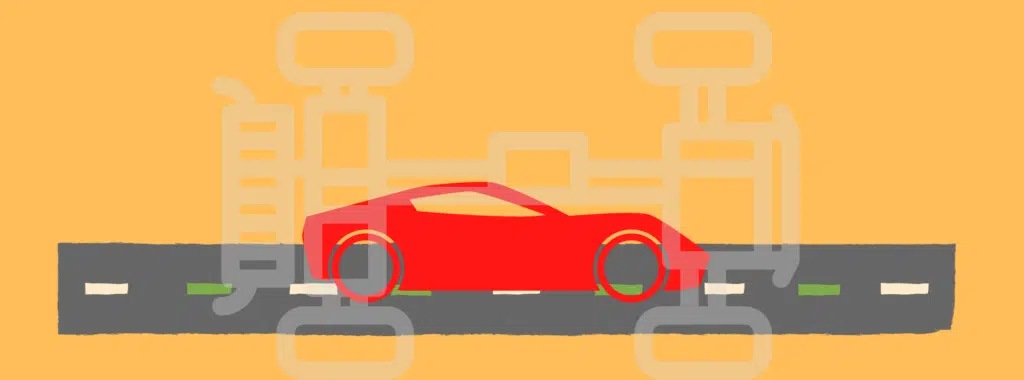
Competing goals seem to find their way into every part of life. Just ask any high-performance car driver. With premium fuels having a hefty price tag and climate change looming large, fuel efficiency in their supercars would be a worthy goal. But how do you retain that coveted speed, sound, and cornering of today’s performance internal combustion engine (ICE) autos? And while all-electric vehicles (EVs) such as the Porsche Taycan can throw you against the seat at the touch of the accelerator, their range of around 250 miles and 30+ minute charges (if you can find a charging station) and less than nimble maneuvering may not yet meet the needs of the exhilarating open road trip seeker.
Enter Dan Dorsch and his high-performance hybrid transmission concepts.
The Framework of a High-Performance Hybrid Propulsion System
Dan’s PhD dissertation at MIT sought to find that happy medium – to maximize both performance and fuel economy. To do this he started with a framework that described all the functions of a drive train, and all the components (“elements”) in a hybrid car that could perform them. By mapping functions to elements, he was able to identify the potentially redundant capabilities of the various components. Then through modeling and bench testing, he proposed the elimination of elements whose functions could be performed by others. (See Figure 1.) Doing so would reduce weight and part count, resulting in both increased performance and fuel economy.
Dan’s challenge was to find a concept that would not only reduce weight but fluidly and quickly shift through the gears to achieve a smooth, spirited drive experience. To meet this challenge, he devised and modeled three clutchless transmission concepts.
Concept 1: Two Electric Motors and an ICE
The first high-performance hybrid concept involved supplementing the high-performance ICE with two electric motors (EMs). The first EM would take on the functions of first and reverse gears and deliver torque to the wheels during shift events. It would also regeneratively brake, and provide supplemental cranking of the ICE in cold weather.
The second EM would offer other key functions. In the absence of a clutch, it would bring the ICE to the proper RPM to match that of the transmission in the new gear, so that coupling can occur. It also would crank the ICE to start, either at a stop or while the first electric motor is providing power to the wheels. To prevent the batteries from completely draining, it would charge the batteries when the car is either parked or driving. In this latter case, the first EM propels the car; meanwhile the ICE turns the second EM, which would act as a generator. Finally, when the car is powered by the first motor from a stop, the second EM could create a load on the ICM to allow pre-spooling of the turbocharger.
The advantages of this design are many. Two fewer gears reduce weight. Torque to the wheels during a gear shift (when the ICE is temporarily disengaged with the drive train) gives a much smoother drive experience. Regenerative braking (EV style) charges the batteries. The weight of the clutch is removed. And the shift event itself has the potential to be faster.
Concept 2: Single Electric Motor and an ICE
Acknowledging that two EMs do not offer enough of a weight tradeoff for eliminating a clutch, Dan tested the idea of a single EM/ICE hybrid clutchless transmission. This concept consisted of two shafts with each four individual gears. These shafts could be powered by either the EM, ICE or both at any given time. Gears on either or both of these could engage with four additional gears, resulting in a possible 32 gear ratios.
This concept was similar to the first, except for three disadvantages. Without the second motor, any turbocharger could not be loaded by the EM for pre-spooling. Also, the motor would not be able to supply torque to the driveshaft during gear shifting. Without the clutch, the motor must provide rev-matching and it can’t simultaneously supply torque. Finally, in the absence of a second motor, battery charging is difficult when driving with frequent stops.
To address this last issue, Dan created a simulation to determine whether this concept’s battery would completely deplete. He assumed the driving conditions modeled by the Artemis Urban Drive Cycle. (This model was developed by 40 European research laboratories studying driving conditions in various scenarios to determine impact on the environment, among other things.) He found that if the batteries recharge when the vehicle is stopped in traffic, or when the vehicle is decelerating and regenerative braking, the batteries would never fully deplete. Therefore, range would not be an issue with this type of high-performance hybrid transmission. However driving performance would not be as smooth as with the first model due to the momentary loss of torque to the wheels during a shift.
Concept 3: Single, Two-Speed Electric Motor and an ICE
Dan’s third design was of a two-speed EM gearshift system that would provide supplemental power to a traditional combustion engine vehicle with an Automated Manual Transmission (AMT). The EM’s lower gear ratio would provide torque up to the tire friction limit for vehicle launch and for low-speed driving. The higher gear ratio would supplement power to the ICE for high-speed driving and provide energy recovery. Its upper limit would be peak vehicle speed. This would prevent the need to disengage the EM at top speeds, as seen in some current high-performance hybrids. The result would be a transmission that could provide the highest power output over the full range of speeds, while still maximizing efficiency.
For this design, Dan focused on the problem of smooth shifting for the EM without a clutch. (The clutch would add too much bulk alongside the ICE drivetrain.) He concluded the friction synchronizers used in current technology to match gear speeds in a shift event would be insufficient due to the large rotational inertia of the electric motor.
Dan’s solution was to use controls to adjust the speed of the motor during a shift event. He tested shifts both with and without friction synchronizers. Before disengaging from a gear, the shift event would start with torque zeroing of the motor. The motor would then decelerate (for an upshift), matching the speed of the new ratio. Once the speed of the new gear was matched to the motor, a sensor would detect the position of the dogteeth in the new gear relative to the motor shaft teeth. When alignment was detected, a shift actuator would conclude the shift event.
Testing the Concepts
To study the validity of his concepts, Dan created benchtop models of his transmissions (See example in Figure 2). He collected data such as shift timing, forces on the various elements, and dog-teeth alignment during shift completion. His results (available at this link here) illustrate interesting tradeoffs of power, added weight, and efficiency.
Tacuna Systems found its way into the mockup of the third concept. Part of the experiment recorded the force of the shift actuator. To do so Dan used an Omega S-type load cell and the Tacuna Systems EMBSGB200 amplifier. This setup allowed a comparison of the forces required to shift with and without a synchronizer.
This test setup isn’t the only place the EMBSGB200 appears at MIT though. These amplifiers are ready to use in MIT’s student-run Maker Space laboratories. One found it’s way into a prosthetic knee research project there as well. MIT chose them because they are readily available, easy to use, work well and affordable. In Dan’s words, “we like them.”
Will We See These High-Performance Hybrid Concepts In Production Cars?
According to his dissertation, Dan developed these designs in partnership with a major high-performance car company. Dan continues to refine his design, noting other concepts are possible using a system-level framework such as the one he created in Figure 1. So sometime maybe in the not so distant future, performance vehicle drivers may achieve that driving nirvana of speed, range and fuel economy in their favorite sportscar.
For more information, check out Dan’s web site at: DanDorsch.mit.edu.