How to Read a Load Cell Data Sheet
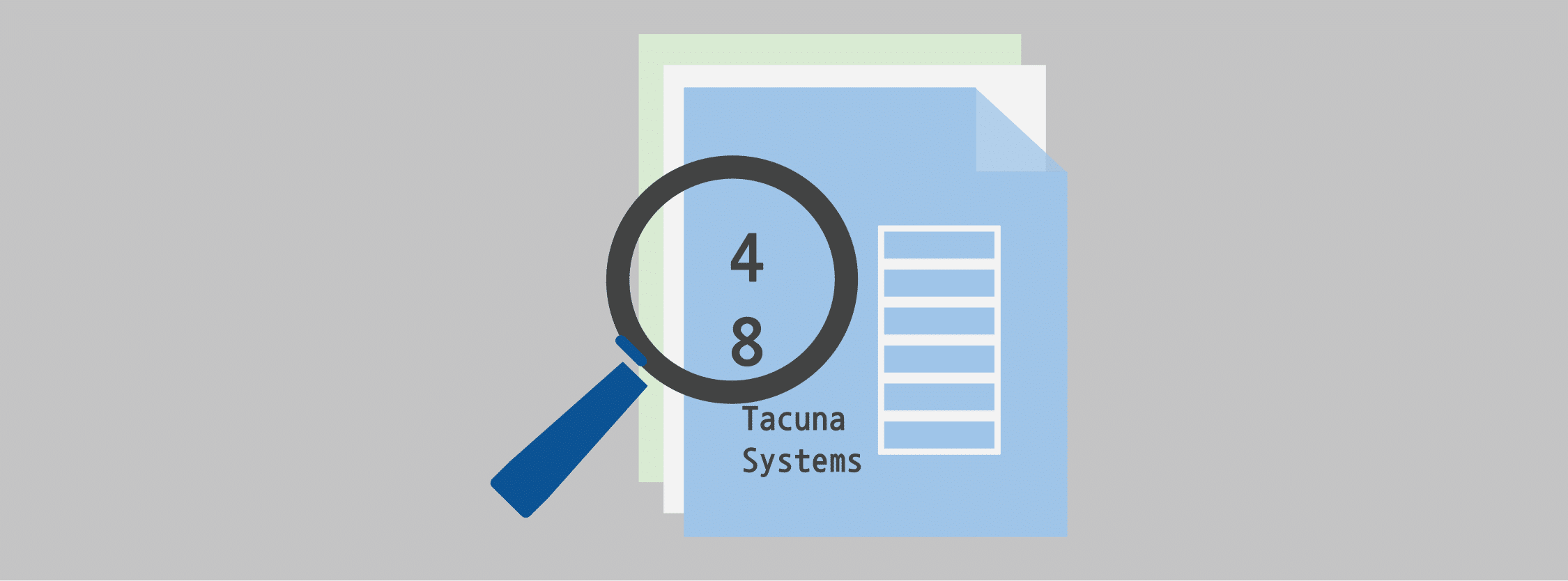
Every load cell on the market comes with a manufacturers’ data sheet. It lists the load cell’s performance capabilities provided by the manufacturer. These specifications help determine if a load cell meets an application’s requirements. They also matter in testing to determine if a load cell calibrates properly or is faulty. Specs on a load cell data sheet generally cover three things: (1) what output voltage can you expect for a given load, (2) how much error can you expect for a given output and (3) how to safely operate the load cell. This article explains how to read a load cell data sheet and interpret some of the most common specifications on it.
Table of Load Cell Specifications
For some terms below, it may be helpful to refer to Figure 6 in our Force Measurement Glossary. Other definitions in this resource may likewise provide some clarity.
Specification | Units | Interpretation | Notes |
---|---|---|---|
Breaking Overload | % | The amount of load over the rated capacity the load cell can withstand before it achieves structural failure. | Expressed as a percentage of rated capacity. |
Combined Error | % | The maximum output voltage deviation from linearity of any load between zero and rated capacity due to hysteresis and non-linearity | Expressed as a percentage of rated output. |
Compensated Temp Range | °C to °C °F to °F |
The temperature range over which the load cell can maintain rated capacity and zero balance within specification limits. | “Compensated” refers to additional gauges that allow the internal load cell circuitry to compensate for temperature variations; without them the operating temperature range would be narrower. |
Creep in 30 minutes | ± % | The maximum deviation of output voltage when measuring rated capacity under identical environmental conditions at the start and end of a 30 minute interval. | Expressed as a percentage of rated output. |
Full Scale Output (FSO) | mV/V | The output voltage the load cell produces at rated capacity, minus the output voltage at minimum load, per excitation volt at the input terminals. | The output voltage at rated capacity is calculated by multiplying the full scale output by the excitation voltage. |
Hysteresis Error | ± % | The maximum deviation of a load cell’s output voltage at any point in it’s measurement range when increasing the load from zero to rated load and returning the load back to zero, taking continuous measurements. | Error is expressed as a percentage of rated output. |
Input Resistance | Ω | The resistance of the excitation circuit. | Measured at the input terminals under no load conditions and an open circuit at the output. |
Insulation Resistance | GΩ | Minimum resistance between the body of the load cell and any electrical wires connected to it. | The larger the insultation resistance the better. |
IP Rating | IP68 | An indication of how resistant an electrical device is to fresh water and common raw materials like dirt, dust and sand. | See this useful graphic. |
Non-linearity | ± % | The maximum output voltage deviation from a theoretical linear input-output plot at any load between zero and rated capacity. The comparative theoretical linear input-output function is the line from zero balance output at no load to output at max load. | Expressed as a percentage of the rated output. |
Output Resistance | Ω | The resistance of the output voltage circuit. | Measured at the output terminals under no load conditions and an open circuit at the input. |
Rated Capacity | t, kg, lb, etc. | Maximum load the device can bear and still operate according to its specifications. | Expressed in mass or weight units depending on the load cell’s scale. |
Recommended Excitation | V | Recommended DC input voltage to the load cell. All strain gauge load cells require an input voltage. | Frequently given as a recommended value and a max value. |
Repeatability | ± % | The ability of the load cell to give the same output for the same load under separate readings under identical environmental conditions. | Given as the maximum observed output voltage deviation as a percentage of rated capacity output voltage. |
Safe Overload | % | The amount of load over the rated capacity the load cell can withstand before it experiences a permanent shift in performance beyond its specifications. | Expressed as a percentage of rated capacity. This metric is important for applications that cause overload due to wind, vibration or other environmental conditions. |
Sensitivity | mv/V | The smallest amount of force detectable by a load cell. | Calculated as the ratio of output voltage at rated capacity load to excitation voltage. The higher this voltage change, the greater the load cell’s resolution will be. |
Service Temperature Range | °C to °C °F to °F |
Temperature range over which the load cell, while in use, will meet the specs in the data sheet. | |
Storage Temperature Range | °C to °C °F to °F |
Ambient temperature range allowable while the load cell is in storage, such that it will not experience a shift in performance beyond its specifications when it resumes service. | |
Temperature Effect on Sensitivity |
±% of Cn/k | The change in sensitivity due to a change in ambient temperature | Expressed as a percentage change in sensitivity per degree Kelvin. |
Temperature Effect on Zero Balance |
± % of Cn/k | The change in zero balance due to a change in ambient temperature. | Expressed as a percentage of full scale output per degree Kelvin. |
Zero Balance or Zero Offset | mV/V | The output voltage the load cell produces per volt of excitation at no load. (It may also appear as a percentage of FSO.) | The output voltage at zero balance is calculated by multiplying the zero balance by the excitation voltage. |
How Load Cell Specifications Apply to Your Project
It may seem somewhat intuitive, but applying the numbers in the spec sheet simply amounts to making sure the performance they describe matches the requirements of your project. Can the load cell operate in the ambient temperatures where it would function? Can it handle the humidity and particulate matter where the weigh system operates? Is the sensitivity appropriate for my output device? (See “How does a load cell’s sensitivity relate to the display or interface I choose?” in our FAQs.) These and similar questions make knowing how to read a load cell data sheet important to any weigh system design.
For more guidance on selecting weigh system components, see our popular article, Choosing the Right Load Cell for Your Job. Or use our contact form to request project-specific consultation.