Force Measurement Glossary
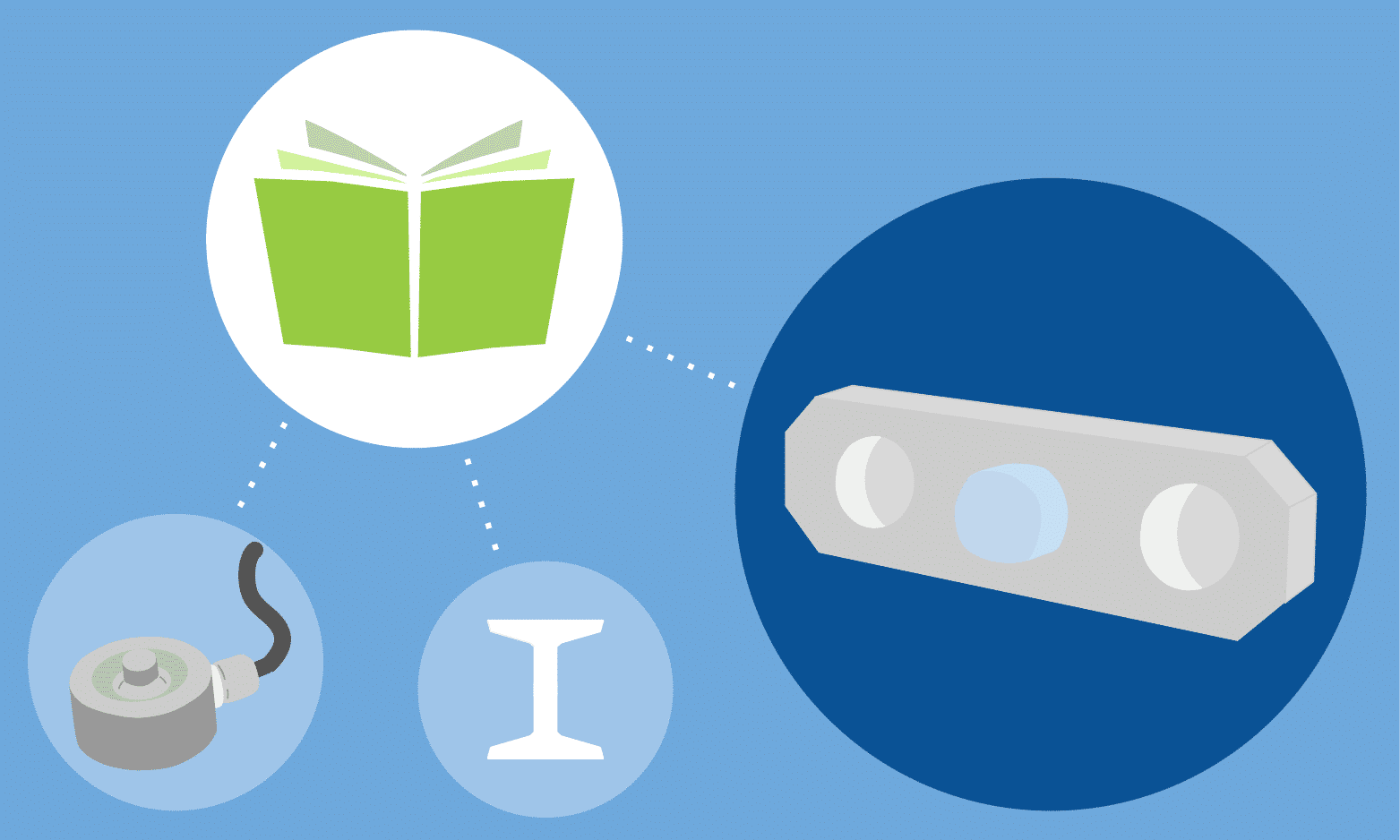
For your convenience, we have defined some common terms related to load cells and force measurement. See our FAQ or Knowledge Base for further information.
A
Accelerometer:
A device for measuring acceleration. The force causing the acceleration of a body is a product of the body mass m and the acceleration a. This physical principle allows the measurement of resultant acceleration caused by vibrating masses under the influence of a dynamic force. See Figure 1 below.
Accuracy:
The degree to which the output of the measuring instrument conforms to the actual value. In engineering, the accuracy of an instrument is the greatest horizontal deviation of the output responses from the calibration line. See Calibrating the Force Measuring System.
Active Transducer:
A transducer that derives its output power from an applied force or energy. It does not require an external electrical excitation to operate.
Air Supply Regulator:
The opening on a pneumatic load cell that regulates the supply of air into the confined space of the load cell’s cylinder. It is located close to the bottom of the load cell, below the diaphragm and controlled by a valve.
Alloy:
A metal made from the combination of two or more metals to give better or the desired properties. Such properties might include greater strength, greater resistance to corrosion, thermoelectric properties etc. They form a majority of the raw materials used to build force measurement instruments. They include Nickel alloys, aluminum alloys, zinc-based alloys, copper alloys etc.
Alloy Steel:
An alloy of steel meeting one of the following properties: (1) the maximum of the range given for the content of one or more alloying element exceeds the following: manganese, 1.65 %; silicon, 0.60 %; copper, 0.60 %; or (2) a definite range or a definite minimum quantity of any of the following elements is specified or required within the limits of the recognized field of constructional alloy steels: aluminum, boron, chromium, up to 3.99 %, cobalt, columbium, molybdenum, nickel, titanium, tungsten, vanadium, zirconium, or any other alloying element added to obtain a desired alloying effect.
Aluminum:
A metallic chemical element. As a pure metal it weighs 28% as much as carbon steel. It is used in load cell bodies, but also in the processing of steel in the following manners. In either the Bessemer, open hearth or electric furnace processes it is used as a deoxidizer, by adding it to the molten steel either in the ladle or in the mold, to remove oxygen and thereby control, or entirely eliminate, the escape of gas (called ”killing”). Aluminum may also be added for the control of grain size, and occasionally as an alloying element.
Ambient Conditions:
The weather or atmospheric conditions in the physical location of the force measurement application. They include temperature, humidity, and air pressure.
American Association for Laboratory Accreditation (A2LA):
The only independent, non-profit, internationally known accreditation body in the US that offers a full range of comprehensive laboratory and laboratory-related accreditation services and training.
American National Standards Institute (ANSI):
A non-profit private organization that oversees the development of voluntary consensus standards for products, services, processes, systems, and personnel in the US. Some of these standards apply to force measuring instruments such as load cells.
Amplifier:
The electronic device that increases the magnitude of the electrical output of a transducer. Most transducers produce output electrical signals that are very small in magnitude, usually in the order of millivolts. This small signal is insufficient for subsequent processes such as system control or even display. Therefore an amplifier must first boost the signal. The most commonly used and efficient amplifier for force measurement is the Instrumentation Amplifier. See Why Do I Need a Load Cell Amplifier (and Other Signal Conditioners)? and Connecting a Force Sensor to a DAQ.
Analog Circuit:
An electronic circuit that handles continuously varying signals called analog signals; it conveys information through changes in current, voltage or frequency. Prior to the digital age, instruments relied on this type of circuit. Modern instruments use both analog and digital circuits to give a more accurate result.
Analog-Digital-Converter (ADC):
An electronic system that converts the analog output of force transducers into digital signals. It consists of elements such as anti-aliasing filter circuits, sample and hold circuits, and digital encoders. Different types exist, such as the flash ADC, successive approximation ADC, and sigma-delta ADC.
Analog Instrument:
The category of measurement instruments that consist of an input transducer, signal conditioners and output elements (such as displays). The input transducer converts the analog signal into an equivalent analog electrical signal that is then amplified, filtered to eliminate electrical noise, and then displayed to indicate the quantity of the analog signal.
Angular Load Concentric:
Description of the orientation of a load being measured, where the applied load’s central axis is concentric with the primary axis of the measuring device at the load application point, but is at an angle to this primary axis. In other words, the axes of the load and of the measuring device intersect at the load application point.
Angular Load Eccentric:
Description of the orientation of a load being measured, where the applied load’s central axis is eccentric with the primary axis of the measuring device at the load application point and at an angle with respect to the primary axis. In other words, the axes of the load and of the measuring device are offset at the load application point.
Anti-Aliasing Filter:
The electronic circuit that bandlimits the output of a transducer to frequencies below the Nyquist frequency. This prevents aliasing when the signal converts back to its analog form by a DAC. Modern digital instruments incorporate this device.
Application Point:
A specific point or surface on a force measuring instrument where the load position is optimal for an accurate reading. Most weighing instruments have a loading platform that applies a distributed load at the appropriate application points. This enables an accurate reading by the force measurement transducer.
Automation:
The creation and application of technology to monitor and control the production and delivery of products and services. This is one of the vast applications of a force measuring instrument.
Axial Alignment:
The alignment of the applied force or load along the transducer’s primary axis. This is very important in the design and installation of an accurate force measurement system. A good force measurement system that measures a single force component should be insensitive to orthogonal force components.
Axial Direction:
The direction parallel to the axis of a body.
Axial Load:
The load that acts parallel to the axis of the platform at its point of application. Figure 2 below depicts both an eccentric axial load (axis of the load and measuring device are parallel, not co-axial) and a concentric axial load (where the two axes are tangent at every point).
Axial Thrust:
A propelling force along the axis of a body that pushes the body in an opposite direction. Examples include the driving force generated by an airplaine’s propulsion system, or forces moving a pogo stick upward. Read the article How to Measure Axial Thrust Using a Load Cell.
B
Bleed Valve:
A valve attached to the body of the diaphragm of a pneumatic load cell. It moves according to the deflection of the diaphragm by the external load, opening and closing the outlet nozzle of the load cell.
Bonded Resistive Foil:
A thin metal strip attached to a structural member of an instrument, or bonded to a non-conductive backing. This technology forms the basis of a strain gauge.
Bourdon Tube:
The tube that connects the outlet of a pressure transducer to a pressure gauge. It transmits the pressure (force) in the hydraulic load cell to the gauge.
Breaking Overload:
The amount of load over the rated capacity the load cell can withstand before it achieves structural failure. Also called “ultimate overload.”
Bulk Micromachining:
The MEM fabrication technique of a subtractive process where etching creates large grooves, pits, and channels on a substrate. Bulk micromachining is primarily used in producing pressure sensors and accelerometers.
C
Calibration:
This term refers to two maintenance actions on a measuring device. (1) It is a comparison of the force measurement instrument’s output to a known standard at manufacture or first use. Or (2) it is the ongoing maintenance of the measurement system to ensure it continues to adhere to that standard. It is also called traceability and it plays a significant role in eliminating systematic errors.
Calibration Curve:
A graph showing how the analytical response of an instrument changes with an applied force or load. There are several methods used in plotting this curve. One is to find the line that best fits a scattered set of readings vs. applied force. For a strain gauge, the curve is the output signal as a function of load.
Calibration Weights:
The sets of known weights used when calibrating a weighing instrument to ensure the accuracy of future results. The sets contain incremental weights measured to a known standard, with the output for each applied weight producing a reading that is plotted to create a calibration curve. See Calibration Weights in our online store.
Capacitive Load Cell:
A load cell that causes the capacitance of the transducer to vary with the stimulus. This change in capacitance is converted into electrically measurable quantities such as voltage. This output is in turn used by a display to show the size of the measured force or load. This type of load cell demands electronic circuitry but its design is mechanically simple and also very sensitive to the input signal.
Center Of Mass:
A hypothetical point near or within a body where the entire mass of the body is assumed to be concentrated in order to model forces acting on the body as a whole. For example, the center of mass of a sphere of consistent density is at its geometric center.
Centrifugal Force:
A force that acts on a body moving in a circular trajectory. The force follows a radial path, away from the center point of rotation of the body.
Certificate of Conformity:
A document granted by a competent authority to an original equipment manufacturer certifying its equipment, products or services meet strict specifications. These specifications include a set of regulatory, technical and safety requirements.
Combined Error:
The maximum deviation of the calibration curve from the linear, theoretical output of a load cell. See Measurement Uncertainty in Force Measurement.
Common Mode Rejection Ratio (CMRR):
In an operational amplifier, it is the ratio of the differential gain to the common mode gain. Simply put, it describes the ability of the operational amplifier to maximize the differential gain at the expense of the common mode gain. It is normally quoted in dB.
Common Mode Signals:
Identical signal components on the inverting and non-inverting inputs of an instrumentation amplifier. Common mode signals are noise signals appearing equally in both input terminals. The input wires are always closely twisted together to help cancel these noise effects. An ideal instrumentation amplifier cancels out common mode signals and amplifies only the differential signals between the two wires.
Compression Force:
The physical force that acts inward on a body and causes it to become compacted. For example, this type of force compresses a spring, causing its physical dimensions and geometric shape to change.
Conformité Européene (CE):
The French for “European Conformity” in English. This marking shows that an instrument complies with the requirements of the European health, safety, and environmental protection legislation.
Corrugated Plate Diaphragms:
Diaphragms that have greater deflections, better linear characteristic curve, and improved sensitivity compared to flat diaphragms. They are commonly used in high-pressure applications, especially in pneumatic load cells.
Creep:
The change in load cell output over time when it experiences a constant load at its application point, under unvarying ambient conditions. In other words if a known constant weight is placed on a load cell for an extended period of time, the output reading of the measurement system may change, or “creep” over time even though no weight is being added or removed and the environment is unchanged. This specification always appears in the load cell’s datasheet. It is typically calculated with a mass at or near rated capacity.
Creep Recovery:
The change of output of a measurement system following a step decrease in the applied force. These step decreases usually are from the rated load capacity to zero-load. In other words, it is the change in the zero-load output of a load cell after the removal of the rated load that has been applied for a specific period of time. It is expressed as a percentage of the rated load capacity over a specific period of time.
Creep Return:
The difference between the initial output of a load cell and the output immediately after removal of a load (usually at or near rated capacity) that had been applied over an extended period of time under constant ambient conditions.
D
Data Acquisition:
The process of measuring physical stimulus (e.g. force, load, weight), converting the result into digital signals and storing them in computer memory for later use or distribution. Modern force measurement instruments usually have digital data acquisition systems that store their output in a drive or transmit this output to a remote display or microprocessor. See Figure 3 below.
Data Acquisition Rate:
Another name for sampling rate.
Data Filtering:
The removal of unwanted noise signals from data signals, to obtain an accurate reading. This corresponds to the “Signal Conditioning” block in the flow diagram shown in Figure 3 above.
Datasheet:
The document that shows the summary of the technical and performance characteristics of an instrument. Engineers use these specifications to ensure the instrument’s performance characteristics match the demands of the system incorporating its use. This document is always provided by the supplier or the OEM.
Dead Load:
The constant load in a structure due to the weight of its structural members or accessories. Also called “minimum dead load.”
Deflection:
The change in the length of a structural member of a load cell when subjected to a load. In a force-balance measuring instrument such as a hydraulic load cell, the load causes a deflection in the diaphragm, which in turn transmits the applied load to the fluid or gas in the confined space. In a strain gauge load cell, the deflection of the structural member causes strain in the strain gauge; this changes the resistance in its circuitry translating the applied load to an electrical signal.
Deformation:
A change in the dimensions (length and area) of a material when subjected to a stress or strain.
Diaphragm:
In force measurement, a thin elastic plate that deforms under an applied load.
Dielectric:
The electrical insulator located between the two parallel metallic plates of a capacitive transducer.
Digital-Analog Converters (DAC):
Electronic circuits that convert digital signals to analog signals. The most common types of DACs are the binary-weighted DAC and the R-2R ladder DAC.
Digital Instrument:
The category of measurement instruments that produces or processes digital signals. Such instruments contain the major elements present in an analog instrument. However, they digitize the analog output from the input transducer using an analog to digital converter. This digital signal is then filtered, multiplexed and/or displayed using a digital signal processor. The instrument may also include a digital to analog converter to generate an analog signal equivalent to, but cleaner than, the original transducer output. Generally, modern-day instruments are digital.
Digital Pressure Transducer:
A pressure transducer whose output is in form of a digital signal. Most pressure transducers display the value of the measured quantity using pressure gauges; however digital types have digital displays, or they transmit output values over distances for remote monitoring.
Drift:
The random change in the output reading under constant loading conditions. It is similar to creep.
Dual In-line Package (DIP) Switch:
An electrical component consisting of a row of manual switches whose combination of on-off positions determines a different electrical output. This type of switch is used to configure a single electrical system for multiple, similar uses. For example, it may change the gain on the same amplifier per different use. The term “DIP switch” can refer to the whole component, or the individual switches in this component.
Ductility:
The ability of a metallic material to undergo plastic deformation when subjected to stress. Plastic deformation is often used as a technique to permanently record an applied force.
Dummy Gauge:
The passive temperature compensation resistor placed on the arm adjacent to the active arm of a quarter-bridge strain gauge setup. The dummy gauge eliminates the effects of temperature on the strain measurement, since identical temperature changes occur in both the active strain gauge and the dummy gauge.
Dynamic Force:
The type of force whose magnitude varies with time. To measure any instantaneous value, a force measurement instrument must have a fast enough frequency response to keep up with the changing force.
E
Eccentric Loading:
A loading condition in which the applied load‘s center of mass is not on the central axis of the load cell’s application point. It is also called offset loading. I t produces a bending moment along with the axial stress generated by the eccentric load. See Figure 2 under “Axial Load“.
Eccentricity:
The distance between the central axis of a transducer and the center of mass of the load.
Elasticity:
The ability of a material to deform while experiencing a load, yet return to its original shape after removing the force. This force may be compressive or tensile. Concurrently, materials have an elastic limit or force which, once exceeded, causes the elastic material to suffer permanent deformation. Also see “necking” below.
Electrical Excitation:
The external electrical energy supplied to the input terminals of a transducer to power its operations.
Electrical Output:
The electrical signal produced as the output of a transducer in response to an applied load.
Electrical Transducer:
A sensor that detects an external phenomenon or stimulus (such as force, pressure, displacement, acceleration) and transforms this into an equivalent analog electrical signal. The output electrical signal is proportional to the applied load; therefore the load’s value is quantifiable.
Electromagnetic Compatability (EMC):
The ability of an instrument or a device to function satisfactorily in its electromagnetic environment without introducing intolerable electromagnetic disturbances to anything in that environment. That is, for an instrument to have EMC, its operation cannot produce electromagnetic fields that interfere with nearby systems’ proper function.
Electromagnetic Interference (EMI):
A form of environmental pollution that can cause malfunctions of electrical and electronic devices, can prevent proper use of the radio frequency spectrum, can ignite flammable atmospheres and has a direct effect on the human tissue. EMC practices help to control various forms of EMI.
Electrostatic Sensitive Device:
Parts or components of a force measurement instrument that can be damaged by electrostatic charges. These charges can build on the instrument operators, tools and other types of conductors in close contact with the instrument. It is abbreviated as ESD. (Note that Electrostatic Discharge is also abbreviated ESD, defined below.)
Environmental Conditions:
Environmental factors that influence the operations of force measurement instruments. They are also called ambient conditions. They include the atmospheric pressure, ambient temperature, and humidity.
Error:
The difference between the actual value of a force, load or weight and the true value. In instrumentation, an error is always expressed as a percentage of the full-scale output. Measurement errors consist of systematic errors and random errors.
Electrostatic Discharge (ESD):
The sudden flow of electricity between two materials at different potentials caused by the imbalance of electrons between the two. The acronym can also mean electrostatic sensitive device, defined above.
Etching:
The process of removing parts of a thin film deposited on a substrate material. Etching is one of the steps in the production of MEMS such as strain gauges. Different types of etching exist, but dry and wet etching are most common.
Excitation Voltage:
Electrical excitation voltage applied to the input of a bridge circuit or passive transducer.
F
Fatigue Life:
The number of total full cycles of force that can be applied to and removed from a measuring device before the measurement uncertainty of further readings will be altered beyond specified limits.
Feedback Amplifiers:
Electronic devices used to amplify the output of a transducer employed in a feedback control system. The transducer measures the output of a process and converts it to an electrical signal. If this electrical signal is weak, the feedback amplifier boosts the signal and compares it with the reference input signal or set point. Feedback amplifiers are of the class of this device known as instrumentation amplifiers.
Field Calibration Methods:
Methods used to determine the repeatability of a measurement process. These methods are very important in applications where precision is more critical than the absolute accuracy of measurements.
Flapper:
The other name for the bleed valve of a pneumatic load cell.
Flexural Bond Strength:
The maximum amount of stress experienced by the bonded material at its moment of yield or fracture. This determines the bonded material’s flexural strength.
Foil Strain Gauge:
A type of strain gauge that consists of a metal foil pattern mounted on an insulating backing or carrier. It is constructed by bonding a sheet of thin rolled metal foil on a backing sheet. The patterns on the gauge are produced by photo-etching.
Force-Balance Systems:
Measurement systems that employ the use of feedback systems to ensure that the output electrical signal is directly proportional to the applied force. These systems give high stability, high accuracy and are suitable for measurement of dynamic and static forces.
Force Calibration:
The process of calibrating a force measurement instrument. See Load Cell Calibration Service by Tacuna Systems.
Force Measurement Methods:
Techniques and principles employed in the design of force measurement instruments. Some common examples are lever-balance methods, force-balance methods, pressure measurement, acceleration measurement and the use of elastic elements. See Force and Weight Measurement Resources.
Force Transducer:
A sensor device that detects an external applied force and transforms it into an equivalent output.
Formal Calibration:
The calibration process that is customarily performed by approved laboratories. The instrumentation used is periodically calibrated and traceable to primary standards; the operators are well trained in calibration techniques, the temperature is controlled, and atmospheric pressure and humidity are accurately measured.
Frequency Response:
The highest sinusoidal frequency component of an applied force that the force measurement instrument can satisfactorily measure to a specified accuracy.
Full-Bridge Strain Gauge Load Cell:
A strain gauge load cell that has four strain gauges fixed into the four arms of a Wheatstone bridge circuit. In Figure 4, the strain gauge arrangement has the two responding to either compression or tensile forces on adjacent arms.
Full-Scale Output (FSO):
The output of the force measurement system at rated load capacity minus the output at minimum load. It is also called the span. Occasionally the FSO refers to the output value at the rated load instead of this difference. (See Figure 6)
G
Gauge Factor:
The ratio of the fractional change in resistance to the fractional change in length of a strain gauge under a load vs unloaded. The mathematical expression is: [ G=frac{ frac{Delta{R}}{R}}{ frac{Delta{L}}{L}} ; or ; G=frac{ frac{Delta{R}}{R}}{ epsilon} ] It is very useful for comparing the quality of strain gauge transducers.
H
Half-Bridge Load Cell:
A strain gauge load cell that has two strain gauges fixed into adjacent arms of a Wheatstone bridge circuit, together with circuit completion resistors. See Figure 5 below.
Hooke’s Law:
A law of physics that states that the force (F) needed to extend or compress a spring by some distance is proportional to that distance. This principle is fundamental to the design of mechanical sensors that measure force through the deformation of an elastic medium. The mathematical expression of the law is F = kx, where k is a constant associated with the material and construction of the spring and x is the distance of extension or compression.
Hydraulic Fluid:
The medium by which pressure generated by an applied load is transmitted from a diaphragm to a pressure gauge. The fluid is housed in the confined space of a hydraulic pressure transducer.
Hydraulic Load Cell:
A type of mechanical, force-balance load cell that measures pressure or load on its loading platform through a piston-cylinder arrangement. A hydraulic fluid housed in a confined space in the body of this cylinder transmits the created pressure through a connecting tube to a pressure gauge. This pressure on the gauge is converted to a reading of the magnitude of the applied load. Alternatively, the pressure output can be converted to an electrical signal by a pressure transducer.
Hysteresis:
The difference between the outputs of a load cell transducer as the load is increased (from zero-load to its rated capacity) and its outputs as the load is decreased (from rated capacity to zero-load). This plot of output vs. load requires that all other factors be constant (e.g., temperature). On a product data sheet, this specification is the maximum deviation of these two curves as a percentage of the rated output.
I
Institute of Electrical and Electronics Engineers (IEEE):
A professional society for individuals in careers associated with electronics and related technologies.
Input Terminal Resistance:
The resistance measured across the excitation terminals of a force transducer at standard test conditions, with zero-load, and with the output terminals open circuited. See How to Test for Faults in Load Cells.
Insulation Resistance Tests:
A troubleshooting technique used when a load cell produces unstable readings and random changes in its zero balance point. This test connects all the load cell’s conductors, then measures the resistance between the connected wires and the load cell body. See How to Test for Faults in Load Cells.
International Aerospace Quality Group (IAQG):
An organization that focuses on the continuous improvement of supply chain processes to deliver consistently high-quality products. A part of its objectives is to establish common quality standards and requirements. These standards apply to various force measurement instruments.
International Electro-Technical Commission (IEC):
An international standards organization that prepares and publishes international standards for all electrical, electronic and related technologies.
International Organization for Standardization (ISO):
A global network of the world’s leading standards bodies and equipment manufacturers. It brings together experts from all over the world to develop International Standards. The organization issues a certificate of conformity to Original Equipment Manufacturers (OEMs).
International Protection (IP) Rating:
An international rating system that defines a product’s or enclosure’s protection against the ingress of solid objects and liquids. See OIML R60-1 or this graphic summarizing the IP rating.
The International Society of Automation (ISA):
A non-profit technical society for engineers, technicians, business people, educators, and students who work, study or have an interest in industrial automation and pursuits related to it, such as instrumentation.
L
Light Emitting Diode (LED):
A semiconductor device that emits light when an electrical current passes through it.
Linear Voltage Differential Transformer (LVDT):
An inductive transducer having a primary winding and two secondary windings of wire around a magnetic core. The primary winding is excited by an AC voltage; the movement of the magnetic core by an applied force then causes a difference in the induced voltages of the two secondary windings with respect to the primary coil. The device uses the basic principles of magnetics to detect a load and then produce an output voltage from the secondary windings that is proportional to the load.
Liquid Crystal Display (LCD):
A visual display used in electronic devices that works by blocking or passing light. The display has a layer of liquid crystal between two layers of polarized glass; applying a current to areas of the crystal alters the alignment of its molecules, affecting its opacity in those areas. A back light beneath the three layers generates the image.
Load:
Forces, deformations, and weights exerted, applied or placed on a surface. A load is a vector quantity, meaning it has magnitude and acts in a specific direction. Figure 6 clarifies terms related to loads applied to load cells.
Load Cell:
A sensor device that detects a physical parameter or stimulus (such as force, pressure) and then produces an output that is proportional to the stimulus. In other words, it is a transducer designed to detect forces or loads. Load cells are generally linear systems. Different types and designs of load cells exist; the most common are hydraulic load cells, strain gauge load cells and pneumatic load cells. See An Overview of Load Cells.
Load Cell Accessories:
Objects or devices that supplement a load cell’s implementation and operation. They include load cell cables and connectors, lifting crane or tension eye bolts, mounting kits and spacers for proper installation and support of load cells. See Load Cell Accessories in our online shop.
Load Cell Indicators:
High-accuracy devices connected to the output of a load cell that amplify and display the value of the measured load (force/weight). They include LCD and LED displays. See Load Cell Readouts, Indicators, Displays and Printers in our online shop.
Load Cell Materials:
The raw materials used to fabricate load cell devices and their parts. These materials include stainless steel, hydraulic oil, phosphor bronze, beryllium bronze, plastics, glass, basic metals, copper-nickel, nickel-chromium, platinum-tungsten alloy. Desired properties such as strength, weight, malleability, corrosion resistance, thermal conductivity, electrical conductivity, machining, viscosity, volatility, thermal expansion determine the choice of material.
Loading Platform:
The interface or surface through which a force/load is applied to a force transducer. The loading platform structure depends on the device’s use; a compression force transducer has upper and lower loading surfaces whereas a tension force transducer attaches the load through upper and lower screw threads. Load cell mounting kits serve as loading platforms to ensure proper force distribution on the device. See the reference article, Load Cell Mounting and Installation Best Practices.
M
Machine Operator:
A skilled technician trained to operate a machine or device such as a force measurement instrument.
Magneto-Elastic Load Cell:
A force transducer designed on the principle that that a ferromagnetic material subjected to mechanical stress undergoes a change in its magnetic properties and the change is proportional to the applied stress. Its properties are advantageous in harsh and electrically disturbed environments.
Manometer:
A device that measures the pressure in a liquid. Conventional hydraulic load cells typically include them.
Maximum Load:
The highest recommended load, less than or equal to the load cell’s rated capacity, for a specific application.
Mechanical Vibrations:
Oscillations in an object or system with respect to an equilibrium point. Different classes of vibration include: free (undisturbed) and forced (disturbed), damped and un-damped (the latter includes negligible vibrations), nonlinear and linear, random (unpredictable) and deterministic.
Microcontroller:
A small computer unit on a single integrated circuit, including a processor, memory and other peripherals. Modern force measurement instruments use these devices for digital signal processing. Microcontrollers have analog to digital input terminals, and digital output terminals. This output can connect to devices that control industrial processes, or to visual display devices.
Micro-Electro-Mechanical-Systems MEMS:
Miniaturized electro-mechanical elements made using micro-fabrication techniques.
Micromachining:
Techniques for fabricating 3D structures on the micrometer scale. This is an advancing trend in manufacturing addressing demands for reduced component size and weight in applications. MEMS are manufactured using micromachining techniques such as photolithography, laser micromachining, and micro-electronic discharge machining.
Minimum Dead Load (MDL):
Same as dead load above. See Figure 6.
Minimum Load:
The smallest load a load cell can accurately measure. It is typically greater than zero, and greater than MDL. See Figure 6.
Modulus Of Elasticity:
A measure of the resistance of a material to elastic deformation under a load. Several elastic moduli exist, including the Young modulus.
Millivolt (mV):
One one-thousanth of a Volt. The unconditioned analog output of an electrical transducer is always of the order of millivolts.
N
Natural Frequency:
The rate at which a body vibrates in the absence of any external force. When a body experiences an initial displacement force and then the force is withdrawn, the body starts oscillating about its initial equilibrium position. The rate at which it continues to oscillate without any external force to keep it in motion is the object’s natural frequency.
National Institute of Standards and Technology (NIST):
A physical sciences laboratory and non-regulatory agency of the United States Department of Commerce. Among its roles is the production of Handbooks with guidelines for various areas of commerce including weights and measures (such as Handbook 44, as discussed in Load Cell Classes: NIST Requirements).
National Physical Laboratory (NPL):
The UK’s national measurement institute.
National Supervision and Inspection Center for Explosion Protection and Safety of Instrumentation (NEPSI):
A government-approved establishment engaged in research and development of explosion protection technology. It provides testing, verification and certification of electrical equipment for use in explosive atmospheres, explosion protection and safety supervision, and assessment of engineering projects.
National Type Evaluation Program (NTEP):
The non-profit organization that tests manufacturer’s devices against US National Standards and government requirements for compliance.
Necking:
A mode of tensile deformation where relatively large amounts of strain permanently localize disproportionately in a small region of the material, resulting in a decrease in the local cross-sectional area at that point (the “neck”). A material will fail or break at the neck when the strain is great enough.
Noise:
In electronics, an unwanted electrical signal present with the desired signal, often caused by electromagnetic interference.
Nominal Displacement:
The measure of deformation of the force transducer when the rated load is applied. It is a factor that indicates the stiffness of the transducer.
Nominal Force:
The maximum capacity (force or load) of the force transducer. It is also known as rated capacity. It is always specified in an instrument’s datasheet.
Nominal Temperature Range:
The temperature range within which the force transducer works properly and meets the specifications in its datasheet.
Non-Linearity:
The maximum deviation of a measuring devices’ response on a calibration curve from its theoretical, errorless straight-line response. It is determined from the calibration plot of increasing loads, and expressed as a percentage of rated output. Theoretically, the output of a force transducer should be proportional to the applied load; however, in practical measurement discrepancies exist and are labeled “non-linearity error”.
Nyquist Frequency:
A frequency that is half of the sampling rate of a digital signal encoder. For example, if a digital encoder samples an analog signal at 200 samples/second, the Nyquist frequency of that analog signal is 100Hz. A digital encoder can represent an analog signal accurately by sampling only if its frequency is below this limit.
O
Operating Range Of The Excitation Voltage:
The range of electrical excitation values within which a transducer can operate at rated capacity and still adhere to its datasheet specifications. When the excitation voltage exceeds this range, a strain gauge generates excessive heat (as it is a resistive element). This alters the expected output.
Organic Light Emitting Diode (OLED):
An LED where the luminescent layer is an organic material. They have advantages over non-organic LEDs including flexibility and transparency.
Organisation Internationale de Métrologie Légale (OIML):
In English, the International Organization of Legal Metrology. It is an intergovernmental body that publishes standards and requirements for measuring systems and components used in international trade. See Load Cell Classes: OIML Requirements.
Original Equipment Manufacturer (OEM):
A company that produces equipment and instruments such as a force measurement device that may be marketed by another manufacturer.
Operating Temperature Range:
The same as the nominal or rated temperature range. It is the range of temperature values within which a transducer can operate at rated capacity and perform satisfactorily within its datasheet specifications.
Orthogonal Forces:
In force measurement, forces perpendicular to the direction of the load (principal axis) measured by the force transducer.
Output Resistance:
The resistance measured on the output terminals of a transducer at a standard ambient temperature at zero-load and zero excitation.
Overload Stop:
The mechanical device designed to prevent overloading or overstressing of the transducer beyond its rated capacity.
P
Passive Transducer:
A transducer that requires an external electrical excitation to operate properly. An example is the strain gauge in a Wheatstone bridge.
Piezoelectric Effect:
The ability of certain materials to generate an electric charge in response to an applied mechanical stress. Materials that exhibit this characteristic either occur naturally or are artificially synthesized. Natural piezoelectric materials include berlinite, quartz, topaz and Rochelle salt, while artificial ones include barium titanate and lead zirconate.
Piezoelectric Force Transducer:
A transducer that uses the piezoelectric effect to measure an applied force or load, as shown in Figure 7. The applied force causes a proportional electrical charge to appear on the faces of the piezoelectric element. It’s an active transducer, meaning it generates the output power entirely from the energy created by the applied force. It doesn’t require external excitation.
Pneumatic Load Cell:
A type of mechanical, force-balance load cell device that measures pressure or load with a piston-cylinder system. It uses a volume of gas housed in a confined space in the body of the cylinder to transmit pressure to a pneumatic pressure dial gauge or a pressure transducer to display the value of the applied load.
Precision:
The reproducibility of the output of a measurement system. A precise measuring system produces the same output for a known force repeatedly over time.
Pressure Transducer:
A device that senses pressure and transforms it into an equivalent output signal, usually in an electrical form. This device can replace the pressure gauge at the output of a pneumatic or hydraulic load cell, offering more accurate readings.
Primary Axis:
The axis along which a load is designed to act on a weighing system. It can be thought of as an imaginary line that intersects the force measuring device’s application point.
Primary Standard:
A standard (that is, a physical representation of a mass, length, or other measurable unit) that is sufficiently accurate such that it is not calibrated by or subordinate to other standards. Primary standards are the authoritative definition or realization of their unit of measure. Standards organizations generally maintain these quantities. For example, in the United States, the Weights and Measures division of the National Institute of Standards and Technology (NIST) maintains primary standards for weights.
Q
Quarter-Bridge Load Cell:
A type of load cell that has a single strain gauge fixed into an arm of a Wheatstone bridge circuit, together with completion resistors and a dummy gauge for temperature compensation. See Figure 8.
R
Random Errors:
Deviations from the expected output of a measuring device that, despite being clearly observed, are difficult to explain. Engineering techniques use probability and statistical tools to estimate random error. These techniques assume that the random signal or error belongs to an ensemble of signals, with each signal having its own probability of occurrence. The probability distribution of this type of error is uniform about the mean output of the measuring device. An example of a cause of this type of error is EMI.
Rated Capacity:
The maximum load a measuring device can bear and still operate within its manufacturer’s specifications. See Figure 6.
Rated Output:
The output signal of a load cell at the maximum load the measuring device can bear and still operate within its manufacturer’s specifications. See Figure 6.
Recalibration:
The process of repeating calibration procedures after initially calibrating a measuring system. The recommended recalibration interval for most systems is about 1 year, to ensure accurate measurements.
Recommended Standard 232 (RS232):
A standard serial data exchange protocol that allows a computer and its peripheral devices to communicate.
Reference Standard:
A force measurement instrument whose performance characteristics are known in relation to a primary standard.
Reliability:
The probability of an instrument performing satisfactorily under stated conditions for a specified period of time.
Repeatability:
The measure of agreement between the results of successive measurements of a constant load, taken with one force measurement system in a constant environment, applying a given force in the same direction (that is, increasing to that load value or decreasing the load to it). Repeatability is measured within a given range of calibration forces applied. It shows the ability of a force measurement system to measure consistently.
Reproducibility:
The closeness of the agreement between the results of the measurements of the same force carried out under changed conditions of measurement.
Resistivity:
The property of a material to resist the flow of electric current through it. See Figure 9.
Resolution:
The smallest change in load that a force measurement system can detect and reliably indicate in its output signal.
Restriction of Hazardous Substances (ROHS):
This often appears as a label on a device. This label indicates compliance with a European Union (EU) requirement restricting the use of certain hazardous substances in electronic equipment.
Rosette (Strain gauge rosette):
A Wheatstone bridge configuration where at a minimum three strain gauges are wired at angles to each other to determine any non-axial components of strain. A rosette measures the magnitude of strain in the “X” and “Y” directions and shear strain. (“X” and “Y” are reference directions relative to the orientation of the strain gauge deemed to be at 0 degrees.) These devices are practical in weigh systems where aligning the force in a in a single, axial direction is difficult.
S
Safe Overload:
The amount of load over rated capacity (expressed as a percent) that can be applied to a force transducer without causing a permanent change in its output specifications. The underlying cause is typically plastic deformation of the transducer’s elastic element. See Figure 6.
Sampling Rate:
The number of instances per unit time (usually per second) that an analog digital converter (ADC) reads the value (such as volts or decibels) of an analog signal in order to convert it to a digital signal. It is usually expressed in Hertz (Hz), or equivalently samples per second.
Semiconductor Gauge:
A type of strain gauge manufactured from strips of either n-type or p-type semi-conducting silicon. It exhibits special characteristics such as high output, no creep or hysteresis, and long fatigue life. Force transducers, accelerometers, and pressure sensors all commonly use semiconductor gauges.
Sensitivity:
The rate of change of the output signal of a load cell as the signal at the input varies, when the load cell is subject to a rated capacity load. The sensitivity of a transducer allows us to predict the output voltage from a known excitation voltage and value of the applied stimulus. Its units for a strain gauge load cell are mV/V.
Shear Force:
A force that acts perpendicular to the longitudinal axis of the body, or equivalently parallel to a cross section of the body. See Figure 10.
Shielding:
Placing a conductive surface around critical parts of an instrument’s circuitry to attenuate any electromagnetic field that couples to it. A good force transducer has a shield wire as its fifth wire terminal.
Shock Resistance Test:
A test on a load cell when its output appears erratic when a load is first applied or removed. It involves checking output readings under excitation and no load when a load cell is tapped, typically with a rubber mallet. Erratic outputs indicate loose connections within the load cell. See How to Test for Faults in Load Cells.
Shunt Calibration:
The calibration of a load cell transducer by the insertion of known shunt resistors into the appropriate arms of its Wheatstone bridge circuit.
Shunt-To-Load Correlation:
The numerical difference between the output readings obtained from shunt calibrations and the known value of the loads.
Signal Conditioning Circuit:
A circuit that performs signal filtering, amplification, and isolation to ensure a more accurate output signal.
Signal-To-Noise Ratio (SNR):
The mathematical ratio of the strength of the desired electrical signal to the strength of electrical interference (also called “noise“) present with that signal. Its unit of expression is decibels (dB).
Span:
The full-scale output of a measuring instrument. See Figure 6.
Stabilization Period:
The required time for a measuring device’s output reading to maintain a steady value accepted as the actual output value.
Stainless Steel:
Any steel containing four or more percent chromium is classified as stainless. However, there are many grades for specific purposes. These grades may contain nickel or molybdenum or both, but always chromium.
Standard Test Conditions:
The stable ambient conditions required for valid test measurements, abbreviated as STC. These conditions include factors such as temperature, humidity, and pressure for force measurements.
Static load:
A load whose size/magnitude does not change with time.
Stiffness:
The ability of a body to resist deformation when a load is applied to it. It is similar to the Young modulus.
Strain:
The ratio of the change in length of a material in the direction of an applied force, to the original length in that direction. Also called engineering strain, it is the response of a material to an induced stress. It is a dimensionless quantity.
Strain Gauge:
A resistive element that produces a change in its resistance proportional to a mechanical strain induced by an applied force.
Strain Gauge Transducer:
A transducer type that uses a strain gauge as its underlying mechanism. The strain gauge(s) is(are) attached to a structural member which undergoes deformation when a load is applied. It is the most common type of load cell in measurement devices across various industries.
Stress:
The internal forces per unit area present in a material exposed to external forces or loads. In the International Standard of Units (SI), its unit of measurement is Pascals; the English System expresses stress in pounds per square inch, or PSI.
Structural Member:
The constituent part of a load cell/force transducer that provides support and housing for other components. The geometric shape of the structural member also determines the category to which the load cell belongs. These categories include beam load cells, disk load cells, S-type, tension link load cells and miniature load cells.
Summing Junctions:
Devices used for summing data output from multiple load cells into a single output. Click here for examples.
System Requirements:
The necessary and desired specifications and standards that the force measurement system must meet for a given application. The user, client or the expert designing system for this given application defines its system requirements. They then choose instruments that best match these requirements to create the system. Quality badges or approvals may help determine system requirement compliance.
Systematic Error:
The error inherent in the operation of a force measurement instrument. It can be quantified or eliminated through system calibration.
Système Internationale (SI) Units:
From the French for International System, this is the conventional name for the metric system of measurements. It is a system of international standards common among all nations and between the different branches of science and technology.
T
Tare Weight:
The weight of an empty container or the loading platform. The results of force measurement readings sometimes include this weight; in those cases tare weight is subtracted to derive the true weight of a measured object.
Telemetry:
An automated communication process that transmits data or information between two geographical locations. In many force measurement applications, this type of transmission enables centralized supervisory data login, signal processing or control of large-scale systems. Telemetry can be electrical or pneumatic. Pneumatic telemetry is used in hazardous areas where an electrical power failure could be disastrous.
Temperature Compensation:
A procedure to eliminate the dimensional changes caused by temperature changes in a transducer. The use of self-temperature compensated gauges or dummy gauges generally addresses these unwanted thermal effects.
Tensile Force:
A pulling force that can stretch or elongate a material.
Tensile Strength:
The capacity of a material to withstand tensile forces.
Thin Film Strain Gauge:
The strain gauge type produced by evaporating thin films of metals or alloys onto an elastic element.
Tolerance:
The allowable maximum deviation of a measured quantity from the standard specifications.
Tool Steel:
A term used for a variety of high-hardness, abrasion resistant steels that are uniquely able to retain shape at increased temperatures. Tool steels have a higher percentage of carbon, of the order of 0.9 to 1.5%, giving it these key properties.
Torque:
The turning effect caused by a force acting on a body at a distance from its center of rotation. It is the product of this force and this distance (essentially a radius). The units for torque are typically foot-pounds or Newton-meters. See Figure 11 below.
Torsional Modulus:
The modulus of elasticity of a material when subjected to a torque force.
Traceability:
Another name for calibration. This term also refers to the tracking and documentation of a product’s origin of materials and parts, product processing, distribution and location of deployment history, or the tracking of data generated when measuring product usage against quality requirements.
Transducer Electronic Datasheet (TEDS):
A manufacturer’s written document included with its transducer products that lists details about its technical and performance characteristics.
Troubleshooting:
The process of detecting, tracking, analyzing and correcting faults in a measurement system. Various recommended standard troubleshooting procedures exist for each force measurement instrument.
True Strain:
This is the natural logarithm of the engineering strain.
U
Ultimate Elongation:
The maximum length reached by a material at rupture when subjected to tensile forces.
Ultimate Overload:
The breaking overload.
Ultimate Strength:
The maximum stress a material can withstand before it breaks.
Unloaded Output Voltage:
The electrical output voltage from the force transducer under zero load or no load.
V
Vibrating Wire Load Cell:
A transducer having a taut ferromagnetic wire that is excited by a drive coil into transverse vibrations. A pick-up coil detects these vibrations. The drive coil and pickup coil have magnetic cores. Once the wire has been excited to its resonant frequency for a given tension, this frequency is maintained by a self-oscillatory system formed between these two coils. The resonant frequency correlates with, and can therefore be used to measure, the applied force on the taut wire at that instant.
Visual Displays:
Visual human interfaces used to indicate either qualitative or quantitative events. A qualitative event is the presence or absence of expected signals. A quantitative event is the value of these signals. LEDs and LCDs are common types of visual displays.
W
Wheatstone bridge:
A circuit configuration primarily used to measure electrical parameters such as resistance, inductance, and capacitance. The configuration incorporates an excitation source, four conductive arms that optionally incorporate passive components, and an output terminal. In order to measure capacitance or inductance rather than resistance, the normal Wheatstone bridge is modified but still follows the same circuit configuration pattern.
Wire Strain Gauge:
The original type of resistance strain gauge, though now widely replaced by foil and thin film strain gauges. It still has applications in high-temperature transducers and stress analysis.
Y
Young Modulus:
The ratio of the stress caused by an applied force acting over an area of a material to the strain. In Figure 12 below, it is the slope of the linear region of each curve. Note the harder a material, the higher the Young Modulus.
Z
Zero Balance:
The default output signal of a transducer when no load or zero-load is applied to it.
Zero Offset:
The difference between the zero-load specified in the instrument’s datasheet and the actual zero load output obtained by direct measurement under zero-load conditions (removal of all weights, loads and dead load).
References
- Difference between Analog and Digital Circuits.
- Definition of Analog Circuits
- Instrumentation Systems
- Mechanical Vibrations
- Instrumentation Reference Book, W. Boyes.
- A Guide to the Measurement of Force, Andy Hunt.
- Handbook of Terms: Commonly used in the Steel and Nonferrous Industries, The Iron Age