An Overview of Load Cells
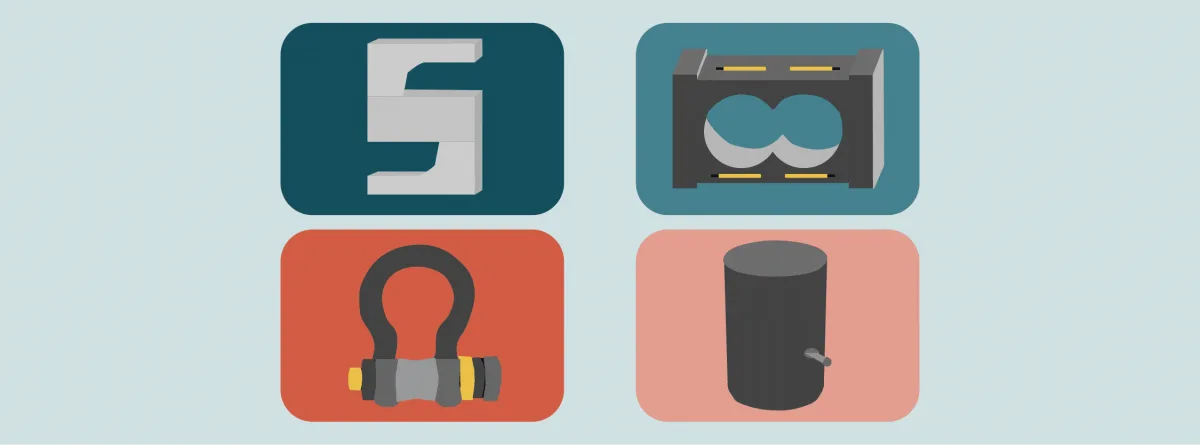
Load cells are precision force measuring instruments. They offer a relatively low-cost, durable, and easy-to-install solution to almost any load measurement need. Load cells have been providing quality measurements in aerospace, agriculture, medicine, industrial weighing and many other applications for decades. Ongoing advancements in load cell technology have further broadened their use. This article explains the different types of load cells that exist, their basic function, and which types are best for various general uses.
Most industrial load cells are the strain gauge type, discussed briefly below. For more specific information on these, see The Versatile Strain Gauge Load Cell in this Knowledge Base. Also, the article, Choosing the Right Load Cell For Your Job, matches specific strain gauge load cell types to their practical applications.
What is a Load Cell?
A load cell is a transducer or sensor that converts the kinetic energy of a force into a quantifiable output such as an electrical signal. Each type exploits some physical property of its component materials to create this measurable output. The strength of the output is proportional to the force (compression, tension, pressure, etc.) applied to the load cell. This output data can then be displayed, stored, or used to control complex systems. Note that without this energy conversion, a force would be impossible to measure, so load cells serve a very important function.
Load cells are most commonly used in industrial weighing applications such as scales. Because load cells can convert forces to electrical signals, they are also often used in control systems where the force on a system affects its behavior. For example, a load cell may measure the tension on a machine that winds cabling on a spool to ensure the system uses a consistent tension throughout its process.
Fundamentally, load cells are in systems that test, monitor, and run industrial machinery, medical devices, aircraft loads, and many other applications.
Types of Load Cells
Several types of load cells exist for varying applications:
Strain Gauge Load Cells
Strain gauge load cells are the most common. Unlike the hydraulic and pneumatic designs described below that convert pressure differentials to measurements, the strain gauge load cell operates through changes in electrical resistance.
Inside each strain gauge load cell is at least one strain gauge device. A strain gauge is a thin wire etched in a back-and-forth pattern onto a non-conductive substrate material with connectors at each end of the wire. The strain gauge functions on the elastic properties of the wire; that is, when a wire is stretched, its length increases and cross section decreases, and when compressed, the opposite occurs. In the tension case, the resistance of the wire will increase, while in the compression case, the resistance of the wire will decrease.
Strain gauge load cells convert this change in resistance to a load measurement. Systems using these types of load cells direct the measured force in a way that causes a deflection (tension or compression) in the strain gauges. Since these devices come in a wide variety of shapes and mounting configurations, the possible load directions (and therefore measuring applications that use them) are numerous. The article, The Versatile Strain Gauge Load Cell explains the internal circuitry (the Wheatstone Bridge) that makes the strain gauge transducer work. This article also covers the various strain gauge load cell shapes.
Strain Gauge Load Cell Components
Strain gauge load cells consist of:
- A loading platform or system to apply the force, \(F_{load}\)
- One or more strain gauges
- An excitation voltage source
- Output wires to measure a change in voltage caused by the change in resistance of the strain gauges
Figure 1 shows a single end beam load cell with these components. The strain gauges at the top of the beam are in tension under the load, while those at the bottom are in compression under the load.
Features, Benefits and Disadvantages of Strain Gauge Load Cells
Strain gauge load cells are the most popular due to their high accuracy, low price point, and general ease of use. They have a high frequency response for dynamic loads and are not sensitive to temperature variations. Because they can fit into a wide variety of load-mounting configurations, they lend themselves to almost any industrial application.
Strain gauge load cells are passive transducers meaning they require an excitation voltage to operate. This can restrict their use in areas of limited electrical supply or in areas where ignition may be an issue.
Hydraulic Load Cells
Hydraulic load cells convert a load to hydraulic pressure. The measured load is applied to a load platform attached to a piston. The piston sits in a closed chamber filled with fluid. When a load is applied, the action of the piston on the diaphragm pressurizes the liquid. The change in liquid pressure is directly proportional to the force applied by the load. This liquid pressure is readable through an attached bourdon tube pressure gauge.
Hydraulic Load Cell Components
Hydraulic load cells have the following components:
- An elastic diaphragm
- A piston connected to a load platform
- Hydraulic fluid which is usually oil or sometimes water
- Pressure gauge or gauges
- A tube connecting the chamber to the pressure gauge
- Steel housing for the assembly
Features, Benefits and Disadvantages of Hydraulic Load Cells
Because the hydraulic load cell design contains no electrical components, this type of load cell lends itself to environments where explosion safety is a concern, or where an outside power source may be difficult to provide.
On the flip side, hydraulic load cells tend to be more expensive than other types, making them cost-prohibitive for certain applications. Hydraulic load cells can typically measure up to 5MN and have an accuracy of about 0.25 to 1.0 percent of full-scale output. Their resolution is typically about 0.02 percent. Because these load cells are sensitive to ambient pressure, the user must reset the readout to zero before each use.
Pneumatic Load Cells
Pneumatic load cells function similarly to their hydraulic counterparts in that they convert fluid pressure into a load measurement. However, the pressurized fluid in a pneumatic load cell is a type of gas, oftentimes air.
The force to be measured is applied to a loading platform on one side of a diaphragm, and a pressure supply regulator introduces a pressurized gas to a chamber on the opposite side of the diaphragm to balance out the force. A nozzle connected to a pressure gauge allows some of the pressurized gas to escape the chamber. The pressure of the gas flowing through this nozzle is measured. This pressure is proportional to the force applied.
Pneumatic Load Cell Components
Pneumatic load cells have the following components:
- A loading platform to apply the force
- A steel chamber filled with pressurized gas or air
- An elastic diaphragm connected to the loading platform that seals the chamber
- An air supply regulator
- Nozzle (bleed valve)
- Pressure gauge
Features, Benefits and Disadvantages of Pneumatic Load Cells
Like their hydraulic counterparts, pneumatic load cells are explosion resistant and are generally used in applications with intrinsic safety concerns. The pneumatic load cell is also tolerant of temperature changes. Finally, this type of load cell is sensitive to small loads. This makes them practical for systems requiring real-time accuracy with the lightest of loads, such as dispensing IV fluids.
Capacitive Load Cells
Capacitive load cells operate on the ability of a material or system to store a charge. They consist of two parallel plates with a gap between them. An electric current is supplied to the plates until a stable charge forms on each: one with a positive charge and the other negative. When a load is applied to one of the plates, the gap narrows causing a stored charge (or capacitance) between the plates. This charge creates the output of the load cell, which is then translated to a load measurement.
Capacitive Load Cell Components
Capacitive load cells consist of:
- A loading platform external to the housing to apply the force
- An insulated housing containing a free moving and a fixed plate
- A dielectric material between the plates (which may be air)
- Electrical wires to the plates
- A rigid rod or connector between the loading platform and the free moving plate in the housing
Features, Advantages and Disadvantages of Capacitive Load Cells
Capacitive load cells are highly sensitive and accurate over a wide range of forces, large and small. They are also rather simple in design, making them more cost-effective than other load cell types. Their ability to be hermetically sealed without compromising their operation makes them a good choice for food and medical weighing applications where hygiene is an issue.
Because capacitive load cells operate using an electric charge they may not be a good choice in flammable environments. Also, some dielectric materials are sensitive to temperature, which can affect the accuracy of the load cell.
Piezoelectric Transducers
Piezoelectric sensors operate based on the piezoelectric effect. The piezoelectric effect is a natural property of materials such as quartz crystal and other ceramics.
Piezoelectricity is produced when this polarized crystalline material is stressed or deformed. The stress then causes a shift in the orientation of the internal dipoles of the material. It is similar to di-electricity, which occurs when a charge develops from a shift of electrons in an insulator. Piezoelectric sensors can quantify force, pressure, and displacement. Metallic electrodes bonded to the surface of the material form a measurable net charge. For proper function, the design must place these electrodes perpendicular to the applied force.
Both compression and tension forces create this piezoelectric effect. Compression forces create an opposite polarity to tension forces. The output voltage is directly proportional to the applied force.
Piezoelectric Transducer Components
Piezoelectric load cells consist of:
- A loading platform or system to apply the force
- Metallic electrodes bonded to the piezoelectric material
- The piezoelectric material
- Output wires to measure a change in voltage caused by the change in charge
Features, Benefits and Disadvantages of Piezoelectric Transducers
A piezoelectric transducer is an active transducer, meaning it does not require an external power source to generate an output signal. This characteristic makes this device desirable in applications where an external power source is inconvenient. However, its output signal does require amplification as it is very small.
The piezoelectric effect happens for dynamic forces. Once a force becomes static, the output of the sensor returns to zero. Therefore these transducers lend themselves to applications requiring the measurement of a transient force.
Piezoelectric transducers are more durable than other load cells, and have a high frequency response.
Conclusion
Load cells are extremely accurate measuring devices used in a variety of applications. Various types exist to suit the application. Tacuna Systems offers a wide product line of quality load cells to meet these application’s requirements. Ask about what innovative solutions we can provide today.