Why Do I Need a Load Cell Amplifier (and Other Signal Conditioners)?
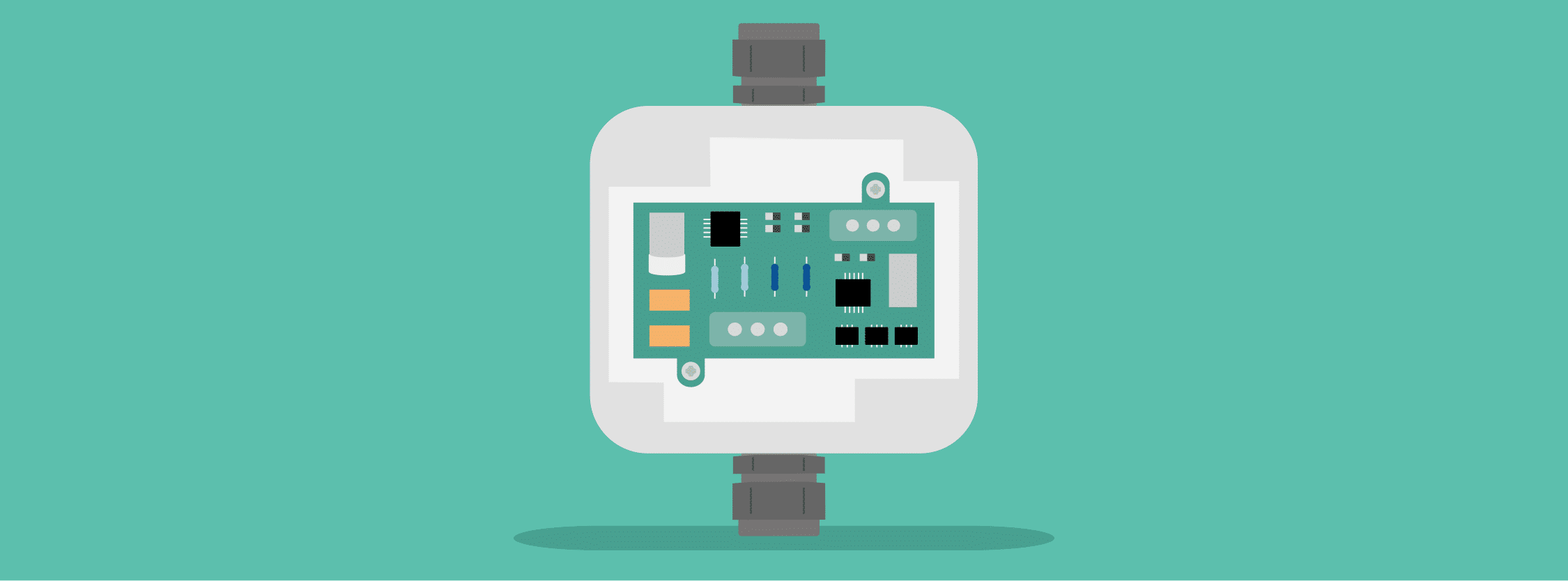
Strain gauge load cells convert the kinetic energy of a force into a quantifiable electrical signal. However, this output signal is very small, in the order of millivolts. At the same time, most weigh systems using these load cells have readout components that need a large, noise free electrical input. (Likewise process control systems may also incorporate load cells and these also require stronger, cleaner signals than is typical of the load cell.) Since the display is what makes the load cell signal human-usable, this difference requires some resolution. The universal solution is to use load cell amplifiers or other signal conditioners to improve the load cell output signal quality before use by displays or control systems.
This article explains the various forms of signal conditioning. But first, it gives a brief background of analog and digital signals, and the process of converting one to the other since signal conditioners depend on this technology. It concludes with a comparison table and buying guide to help the reader select the right product for their project.
Analog and Digital Signals
Most load and force measurement sensors or transducers generate an analog signal output. Therefore, signal processing is traditionally analog.
However, with the availability computing, wireless Internet, and faster processing than ever before, signal processing systems are increasingly digital. These digital load cell conditioners include software usable in real-time.
Analog processing remains faster, but digital processing often delivers more accurate results. Digital signal conditioning also allows for easier troubleshooting, adjustment, and tuning. Because each processing method has its advantages, systems often incorporate both. In this case, analog-to-digital and digital-to-analog conversions become part of the signal processing.
Analog-to-Digital Conversion
Analog to digital converters, or ADCs, appear in applications when digital signals are simpler to manipulate or process. We are familiar with applications such as music recording, or photography, where converting light or sound to digital signals. The digital format gives tremendous flexibility in shaping the creations of these industries. In the same way, ADCs are useful in converting measurements of a load cell into digital format.
ADCs sample the amplitude of a signal at discrete points in time to convert it to a digital signal representing the magnitude of the analog measurement. The arrows in Figure 4 below represent each moment data is sampled. The analog input, shown as the light green curve, is a constant stream along the time axis. The output samples are digitized into a stream of bytes.
Signal Accuracy and Resolution
Signal sampling limits the allowable bandwidth, or range of frequencies that can be accurately represented by a digital signal. This is the “Nyquist limit,” and is equal to half the sampling frequency. That is, if a ADC samples at a rate of 120 samples per second, the highest input frequency that the ADC output can accurately represent is 60 Hz.
Because the digital output is no longer a constant signal, operators must pay careful attention to the speed of conversion of the analog signal. The number of digital bits used to represent the amplitude is also important. These will determine the resolution and accuracy of the digital signal.
A bit is a binary digit, or logical value, that represents some unit of information. This is often implemented on two-state devices. An analog-to-digital converter will typically use at least eight bits but can use as many as 12. The digital bandwidth is defined by the resolution of these available numbers.
28 = 256 So the resolution of the 8 bit sample is 1 part of 256
212 = 4096 So the resolution of the 12 bit sample is 1 part of 4096
Signal Conditioning
As previously implied, signal conditioning is the process of taking raw load cell electrical output and turning it into useful data. It can be one or more of these functions: amplification, attenuation, isolation, linearization, or other types of filtering.
When signal conditioning is part of a measuring system, its output will have these three qualities: (1) Ideally it will be free of noise/unwanted frequencies (through filtering); (2) It will be in the appropriate format; (3) The signal will be large enough to detect.
Amplification
Most of the time, the raw output signal of a load cell is too weak to read without amplification, being of the order of 100mV or less. This makes the signal rather susceptible to ambient electrical noise (such as electromagnetic interference).
How does the load cell’s initial signal change with an instrumentation conditioner or amplifier? The load cell output is amplified from 0~36 mV to either 0-10V or 4-20mA. Amplifiers typically use DC power (24V) and can drive ~ 300Ω load cells connected directly. Many handle one or two devices alone but can connect to more load cells at a time via junction boxes. (See Load Cell Summing: Junction Boxes, Signal Trim and Excitation Trim.)
Analog Amplifiers
Typically analog amplification happens through an operational amplifier, also known as an op-amp. Op-amps are electronic devices with two input terminals: the inverting and non-inverting ends. As Figure 2 shows, the raw signal connects to the inverting side with one resistor; the non-inverting side connects to ground. A feedback path connects from the output terminal, with a second resistor, to the inverting terminal.
The output signal is related to the input voltage through the equation below. Therefore the amount of amplification is based on the values of R1 and R2.
Operational Amplifier Relational Equation
\(V_{0}=\frac{R_{2}V_{i}}{R_{1}}\)
Instrumentation amplifiers, such as the ones used with load cells, require the amplification of extremely low-level signals. They often contain a combination of as many as three op-amps to generate the necessary, increased output amplitude.
Certain applications, like accelerometers, require the amplifier to have a high-frequency response, to prevent distortion.
Digital Amplifiers
Digital amplifiers, as the name implies, increase the magnitude of a digital signal rather than an analog one. Therefore the transducer’s analog output must be converted to digital through an ADC before any digital amplification occurs. Digital amplifiers simply multiply the sampled values by a fixed constant to amplify the signal.
Attenuation
Attenuation is similar to amplification, but instead of increasing the signal amplitude, attenuation decreases the signal amplitude. This is necessary when the voltage is beyond the range of the analog-to-digital converter. These devices typically become necessary when measuring signals greater than 10V.
For both signal amplification and attenuation, the digital signal is multiplied by fixed constants; this mathematically changes the amplitude of the output.
Isolation
Signals outside of the voltage range of the device can cause damage to equipment and be dangerous to operators. Isolation is common when there is a need to protect the measurement system from voltage spikes. It is also the solution to break ground loops, block surges, and reject high voltages.
Various methods exist for isolating voltages, including creating physical barriers for signals, and using isolation amplifiers. The specific application, and the driving reasons for the need for isolation determine the method used.
Signal Linearization
Signal linearization converts the non-linear output of a sensor or transducer to a linear function of the desired output. This is necessary for instruments when the signal output does not have a linear relationship to the desired measured output; for example, a transducer’s output may not be quite linear vs. the input force or load. Signal linearization is achieved with signal conditioners such as op-amps or through digital software. Devices that measure temperature, like thermocouples, often require linearization.
Bridge Completion
Bridge completion forms a four-resistor Wheatstone bridge when using a quarter or half-bridge sensor. The Tacuna Systems precision strain gauge amplifier/ conditioner can provide this completion with high-precision resistors. This device can detect small voltage changes across the active sensors connected to it.
Signal Filtering
Signal filtering is a form of conditioning that removes a specific type of signal, such as a specific frequency, from the raw source signal. For instance, if an operator only wants to measure the high-frequency portion of a load cell output, they might filter the erroneous low-frequency signals that skew results.
Signal filtering is possible both digitally and through analog circuits. The most common filters are high-pass, low-pass, band-pass, and notch filters. As their names imply, these filters allow or deny the passage of high, medium, or low-frequency signals from the raw source signal. The range of frequencies that pass through is the “pass-band,” while the denied range is the “stop-band.”
A passive filter is a signal filter consisting of only passive elements such as resistors, capacitors, inductors, and transformers. This type of filter is useful because it does not require external power. Also it is typically more stable than an active filter.
An active filter consists of active elements such as an amplifier, and therefore it requires a power source.
Implementing a Load Cell Amplifier or Conditioner
While selecting the appropriate load cell model for an application is important, selecting a signal conditioner is equally critical. The wrong amplifier or conditioner can distort the load cell measurements. Likewise, properly operating the load cell amplifier is critical to obtaining high-quality, accurate readings.
For best results in using signal conditioners, follow these three guidelines.
- Always follow the manufacturer’s operation manual,
- Ensure that operators receive proper training prior to installation,
- Contact your vendor should questions or concerns arise while operating products.
Tacuna Systems is readily available to answer any design or implementation questions regarding our amplifier and conditioner products. See our “Featured Customer Projects” section to see the scope of projects we’ve assisted with. (See especially, Next-Gen Transmissions for High-Performance Hybrid Cars, and Measuring Contact Forces on Soft Materials for Medical Robotics and Other Applications for test projects using the Tacuna Systems EMBSGB200 amplifier.)
Connecting and Installing a Load Cell Amplifier
The following is an example of connecting an ANYLOAD load cell amplifier:
- The input voltage should connect to 24V DC power and the ground terminal to the ground.
- The load cell connects to the amplifier through the positive(+) and negative(–) excitation terminals, and to the positive(+) and negative(–) output mV signal terminals.
- The output from the amplifier connects to either the current output for a signal of 4~20mA or a voltage output signal of 0~10V.
- To calibrate the conditioner, remove any load from the transducer and adjust the variable resistor to an output of 0V or 4mA. To calibrate the full span, place the entire load on the transducer and adjust its variable resistor to an output of 10V or 20mA.
The load measurement system will be fully functional and ready to operate. Re-calibrate the device frequently and whenever the output readings change, or the signal is abnormal. Most load cell signal conditioners should operate from 10°C – 40°C, or 15 – 100°F, and below 90% relative humidity. However, always review the product specs before operating in high and low-temperature environments.
Lastly, contact the supplier for setup assistance, calibration assistance, and troubleshooting.
Tacuna Systems Load Cell Amplifiers: Comparison and Buying Guide
This section provides a comparison table with each amplifier and signal conditioner product Tacuna Systems carries.
Device | Tacuna Systems EMBSGB200-M | Tacuna Systems EMBSGB200-C | Tacuna Systems EMBSGB200-X | ANYLOAD A1A-22 | ANYLOAD A1A-D25 | ANYLOAD A2A-D2 | ANYLOAD A2P-D2 |
---|---|---|---|---|---|---|---|
Load Cell Compatibility | Any strain gauge type | Any strain gauge type | Any strain gauge type | Any strain gauge type | Any strain gauge type | Any strain gauge type | Any strain gauge type |
Field Calibration Required? | No | No | No | Yes | Yes (9pt multi-section, non-linear calibration) | Yes | Yes |
Bridge Completion | Yes: quarter and half | Yes: quarter and half | Yes: quarter and half | No | No | No | No |
Excitation voltage to LC | 5V | 5V | 5V | 12V | 5V | 5V or 12V (settable) | 5V or 12V (settable) |
Input Signal | 100mVDC | 100mVDC | 100mVDC | 0mV-30mV | 0mV-30mV | 0±36mV | 0±36mV |
Output Signal | 0-5V analog | 0-5V analog / 4-20mA | 0-5V analog or 12 bit digitized with ADC | 0-10V | 0-10V | 0±10V | 0±10V |
Noise Elimination Filter | Two low-pass (corner frequency 68Hz with 350Ω bridge or 104 Hz with 120Ω bridge) | Two low-pass (corner frequency 68Hz with 350Ω bridge or 104 Hz with 120Ω bridge) | One low pass antialiasing filter; corner frequency 200Hz | ~400Hz | 2.3Hz | 16Hz | |
Gain Setting | Discrete preset values selectable with DIP switch | Discrete preset values selectable with DIP switch | Programmable via RS232 | Potentiometer | Programmable via RS232 | Potentiometer (to adjust span) and combination of DIP switch and excitation voltage settings | Potentiometer (to adjust span) and combination of DIP switch and excitation voltage settings |
Offset Adjustment | Potentiometer | Potentiometer | Programmable via RS232 | Potentiometer | Programmable via RS232 | Potentiometer | Potentiometer |
Capacity | With junction box up to: 16 x 700Ω 8 x 350Ω | With junction box up to: 16 x 700Ω 8 x 350Ω | With junction box up to: 16 x 700Ω 8 x 350Ω | Single 350Ω or With junction box up to: 8 x 700Ω 4 x 350Ω | Single 350Ω or With junction box up to 4 x 350Ω or greater | Single 350Ω or With junction box up to: 8 x 700Ω 8 x 350Ω 4 x 350Ω | Single 350Ω or With junction box up to: 8 x 700Ω 8 x 350Ω 4 x 350Ω |
Overall Dimensions | 1in x 3in x 0.5in | 1in x 3in x 0.5in | 1in x 3in x 0.5in | 3.7in x 2.5in x 1.4in | 3.7in x 2.5in x 1.4in | 4.02in x 5.0in x 1.14in | 3.9in x 2.8in x 2.6in |
Enclosure Material | ABS (optional) | ABS (optional) | ABS (optional) | Aluminum Casting | Aluminum Casting | Aluminum Casting | PVC |
Enclosure Ingress Protection | IP40 | IP40 | IP40 | IP66 | IP66 | IP66 | IP40 |
Enclosure Installation | None – Tabletop or double-sided tape | None – Tabletop or double-sided tape | None – Tabletop or double-sided tape | Screw mounting holes within enclosure | Screw mounting holes within enclosure | GORE breather vent and capacitive screws | Screw mounting holes on flanges external to enclosure |
Summary
The raw signal from a load cell is generally weak and subject to environmental conditions that can introduce signal noise. This noisy signal is difficult for an interface to accurately convert to a load measurement. Signal conditioning, including amplifiers, correct this output to increase the overall accuracy of the force measuring system. The output of the measuring system will ideally be: (1) noise-free, (2) in the appropriate format (analog or digital), (3) filtered for unwanted signals, and (4) strong enough to be usable by the receiving display, storage device, or control system.
To see an interesting example of our Tacuna Systems EMBSGB200 Amplifier at work, see Next-Gen Transmissions for High-Performance Hybrid Cars in our “Featured Customer Projects” section of this Knowledge Base!
References
- Measurement and Instrumentation Principles, 3rd Edition Alan S.
- ANYLOAD A2P-D2 Load Cell Amplifier Product Manual (v1704)
- The Engineer’s Guide to Signal Conditioning, National Instruments